A tape measure, chip brush, and dental tools hang on a wall. This isn’t the beginning of a joke but rather important tools used in our foundry as we make sculptures seen all around the world. Artisans from each department at Bollinger Atelier were asked what tool was most useful to their process and why, these are their responses below.
DIGITAL: Tape Measure
Measure twice, cut once. Digital works with measurements. Whether we are collecting data points for a piece through laser scanning, or creating tool paths for the CNC machine; we have to measure things well. I often think that we are the coordinators of information. While the programs we use help us immensely in figuring out specifics, it is still up to the user to instruct and input the proper information for computers to follow. We measure before milling, we measure before cutting foam blocks, we measure where to put our screws, we measure before waterjet cutting, and we measure again once the pieces are put together. All of these parts require that we know how to gather accurate data and oftentimes a Tape Measure does the trick.
Daniel Mariotti, Digital Artisan
MOLD: Chip Brush
The chip brush is one of my most important tools. Broad strokes and tiny dabs. The chip brush can catch extreme detail; a perfect replica of all forms. I can take an impossible corner and bend it to the laws of draft. This brush smooths, captures, thickens, cleans, and creates a lasting form of information captured. Even though it’s only a one-use tool, it’s creating a mold that can last for decades to come.
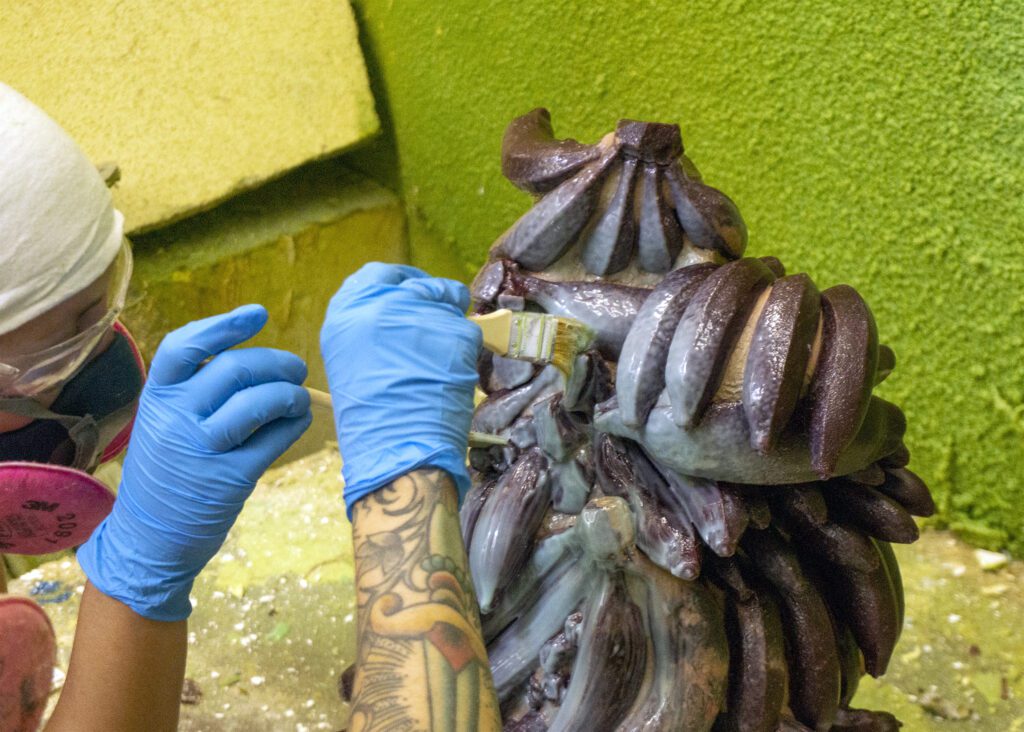
WAX: Dental Tools
When wax is first pulled from a mold it has artifacts, imperfections left by the mold, or signs of turbulence introduced during the rolling process. These imperfections can show up as seam lines, positive bubbles, negative bubbles, and delamination. The wax artisan will look at the wax, assess the work to be done, and select the tool for the job. Wax-specific tools do not exist, so the artisan’s co-op tools and terms from other disciplines. Ceramic loop tools of varying sizes are used for carving. Metal sculpting tools made for oil-based clay are used for adding and subtracting wax. Rasps used in plaster and stone carving are applied, and even fine picks used by dentists are utilized. These tools combined with heat from a torch are applied subtly to manipulate or “dress” the wax casting’s surface. Once a hole has been filled or a positive has been taken down, the artisan uses these tools to re-create the artist’s original texture. The “mark” of a good dressing job is that there is no mark. With the knowledge and skill, artisans should be able to dress a wax, removing any sign of the molding and rolling process, leaving a “perfect” wax replication of the artist’s original
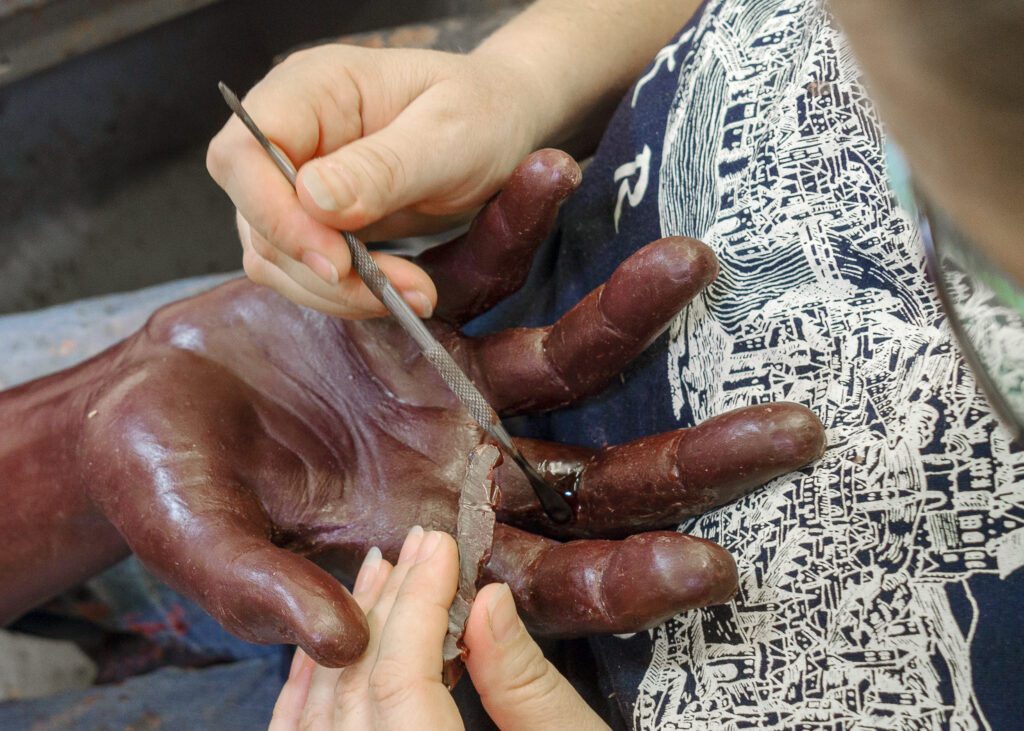
SHELL: Sand
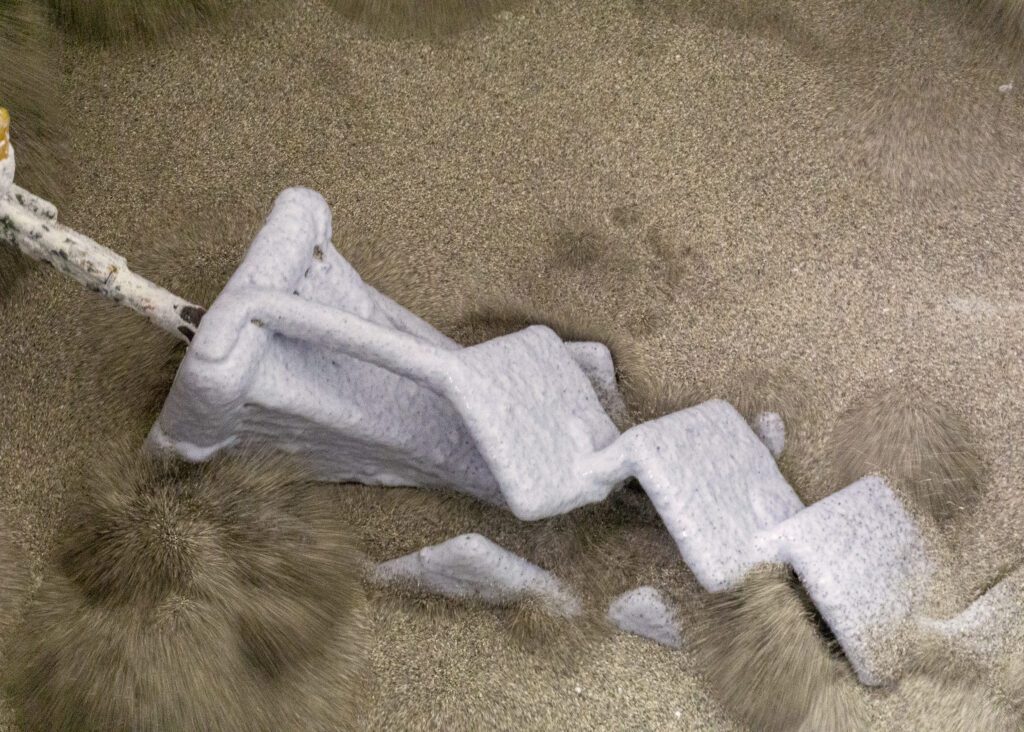
We use sand like a textured glue between layers of ceramic. “A” sand helps create a latticework that keeps the slurry together. “B” sand reinforces and bridges the mechanical locking of “A” to “Stucco” sand. “Stucco” is an aggregate that strengthens the whole piece and creates a thickness that allows for the handling of material. Together, they create the perfect breathable mold ready to have 2000+ degree bronze poured while having the strength and stability to pour over 55,000 lbs. of metal a year.
Daniel Easley, Shell Artisan
POUR: Small Crucible
The Crucible: the interim glowing pot of impending permanence. Within the whirlwind fire, within refractory walls of the furnace lies a chaotic bowl of joy, terror, and immanent potential. Once drawn from the furnace, the race against time begins and the choreographic layout of the foundry becomes heavily apparent. One false step can cost you everything. Every last drop must be poured and along with it comes an earned sense of relief. You don’t just use a crucible, you survive it.
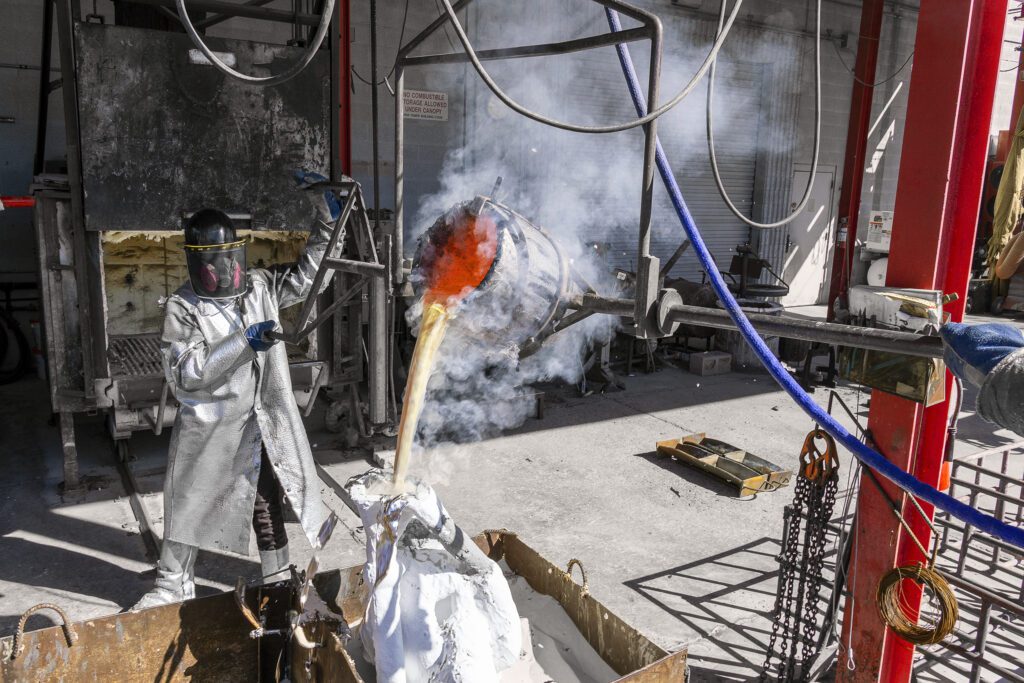
METAL: Variable Speed Angle Grinder
There are many tools used by Bollinger Atelier artisans in the metal shop to accomplish the often unglamorous business of “chasing”. Chasing is where, to quote Tom, we “turn sow’s ears into silk purses” and involves many processes, instruments, and techniques that each artisan develops to achieve the high standard of quality we are known for. Rather surprisingly, when asked if there was one tool that was the most indispensable and versatile, consensus amongst the metal shop artisans was reached quite quickly. The variable speed angle grinder was considered by all of us to be crucial in all aspects of production. What may appear as a generic (slightly crude) power tool performs many vital functions in the hands of artisans. Subtle speed adjustments, “touch”, attachment modifications invented by long-serving BA artisans – help push and pull a piece into the wow factor associated with artwork made at Bollinger Atelier.
Adam E Mendelsohn, Metal Artisan
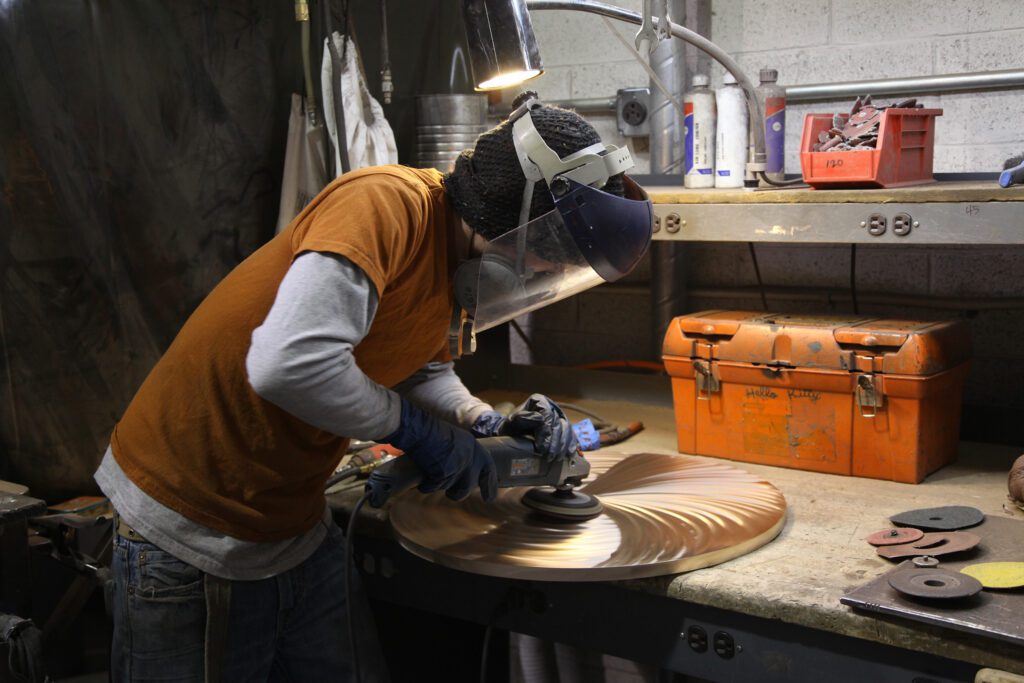
PATINA: Patina Torch
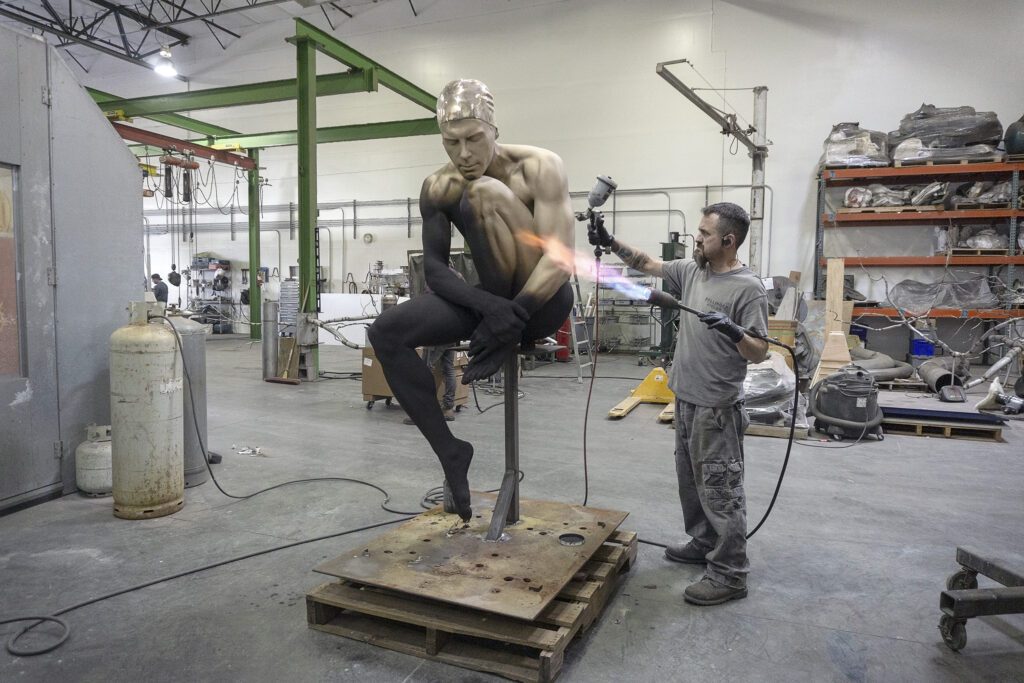
Of all the tools a patina artist carries on their belt, none is more indispensable than the torch. Many types of metals can and will form a natural patina over time if left alone. However, it is the job of the patina artist to accelerate and manipulate this naturally occurring oxidation process by coaxing colors out of the metal in a dance of flame and chemical application. With the exception of paints and dyes (cold patina), a patina is oxidation forming on the surface of the metal. The patina torch accelerates the oxidation process by raising the metal’s temperature and therefore increasing the energy of reactant molecules in the metal. A patina artist takes advantage of this acceleration by manipulating the temperature with combinations of various chemicals to produce colors and patterns that would not naturally occur in nature.
From the precision of the tape measure in digital modeling to the versatility of the variable speed angle grinder in metalwork, each tool plays a pivotal role in transforming artistic visions into tangible sculptures. This collective expertise underscores Bollinger Atelier’s commitment to excellence in the art of sculpture fabrication.
Are you passionate about the art of sculpture and eager to contribute your skills to a dynamic team? Bollinger Atelier is seeking dedicated artisans to join our community. If you’re interested in collaborating with professionals who value precision, creativity, and craftsmanship, we invite you to apply. Email kim@bollingeratelier.com for further details.